
So gelingt effiziente Instandhaltung
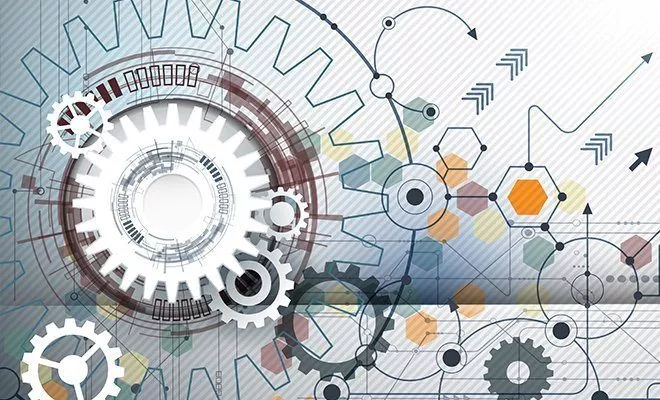
Wahrscheinlich verschwenden Ihre Mitarbeiter in der Instandhaltung gerade wertvolle Arbeitszeit. Und Sie tragen die Verantwortung.
Denn neben der eigentlichen Instandhaltung müssen Ihre Mitarbeiter Formulare ausfüllen, Falschmeldungen angeblich defekter Maschinen prüfen und absurd zugeordnete Instandhaltungsobjekten suchen. Das alles kostet Zeit. Unnötige Zeit.
Morgens halb vier in Deutschland in einer Versandabteilung in Halle 4711. Maschinenstillstand. Das Förderband bewegt sich nicht mehr. Es muss schnell eine Lösung gefunden werden. Zeit ist hier bares Geld. Also wird der Prozess der Problemfindung in Gang gesetzt.
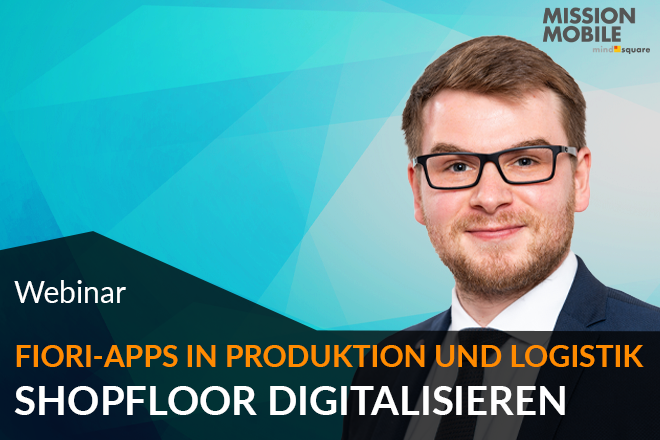
Bisheriger Prozess: Fehlerbehebung beauftragen
- Ein Produktionsmitarbeiter informiert den Abteilungsleiter.
- Dieser ruft beim Helpdesk an und gibt die Fehlermeldung auf.
- Leider ist der Leiter der Versandabteilung auch nicht in der Lage, die Ursache genauer zu identifizieren.
- Die Störung wird somit mit dieser einen spärlichen Information an den zuständigen Disponenten der Instandhaltung weitergeleitet.
- Der Disponent entscheidet sich dazu, einen Auftrag anzulegen, kann diesen aber leider nicht ausreichend spezifizieren.
- 20 Minuten später kommt Ihr Mitarbeiter Maurice Meyer ins Büro und überprüft die Auftragsliste.
Erst nach diesen 6 Schritten ist der Vorfall an einen zuständigen Mitarbeiter gemeldet und erst jetzt kann mit der eigentlichen Problemlösung begonnen werden.
Bisheriger Prozess: Problem lösen
- Herr Meyer war gerade in Halle 4712, keine 50 Meter von der Versandabteilung in Halle 4711 entfernt. Er marschiert die 15 Minuten zur Halle wieder zurück.
- Auf Verdacht, und um Zeit zu sparen, nimmt Herr Meyer einen fünfminütigen Umweg in Kauf und nimmt direkt eine neue Benzinpumpe aus dem Lager mit.
- In Halle 4711 angekommen, überprüft er das Förderband. Herr Meyer stellt fest, dass es sich bei dem Defekt (leider) nicht um eine kaputte Benzinpumpe, sondern um einen gerissenen Keilriemen handelt.
- Sofort macht er sich auf den zehnminütigen Rückweg in das Verbrauchslager auf. Es vergehen weitere 15 Minuten, bis ein Lagermitarbeiter Herrn Meyer einen neuen Keilriemen inklusive einer Warenausgangsbuchung übergeben kann.
- Erneut zurück in Halle 4711 verbaut Herr Meyer den neuen Keilriemen und nimmt das Förderband wieder erfolgreich in Betrieb.
- Abschließend fehlt nun noch die Rückmeldung des Auftrags im System über die Desktop-Arbeitsstation im Büro. Diese beinhaltet mitunter Zeiten, Vorgänge, Materialverbrauch – alles hat sich Herr Meyer schon nebenbei notiert und muss es jetzt erneut eingeben.
Es braucht 6 weitere Schritte und viele unnötige Gänge, bis der Fehler behoben ist. Insgesamt werden also 12 Schritte von der Fehlerfeststellung bis zur Lösung gebraucht.
Dabei könnte es so einfach sein.
Neuer Prozess: Problemlösung mit minimalem Aufwand
Sehen wir uns an, wie das gleiche Fehlerszenario mithilfe von smartem Technologieeinsatz in einem Bruchteil der Zeit gelöst werden könnte.
- Die Förderbänder in Halle 7 stehen. Ein Produktionsmitarbeiter legt mittels Handheld direkt eine Störung an und fügt ein Foto des Antriebstrangs bei. Zeitgleich ist Herr Meyer in unmittelbarer Nähe in Halle 8 kurz vor der Fertigstellung einer Instandhaltungsarbeit.
- Der Disponent erhält via PUSH-Nachricht die Information über die Störung in Halle 7. Er vermutet auf Basis des angehängten Fotos einen Defekt mit dem Keilriemen und bittet den Produktionsmitarbeiter ein detaillierteres Foto zu schicken. Die Vermutung bestätigt sich. Der Disponent erstellt den Auftrag mit den entsprechenden Details und bekommt direkt den Vorschlag: „Herr Meyer ist in der Nähe von Halle 7“.
- Herr Meyer ist gerade auf dem Weg ins Büro und bekommt via PUSH-Nachricht den Auftrag zugeteilt. Er prüft diesen und begibt sich auf direktem Weg ins Verbrauchslager. Dort angekommen, geht Herr Meyer zum Keilriemenlager, scannt einen Keilriemen und bestätigt diesen auf seinem Handheld . Die Warenausgangsbuchung wird automatisch im Hintergrund verarbeitet.
- In Halle 7 scannt Herr Meyer das Förderband (den technischen Platz) und verbaut den neuen Keilriemen. Im Anschluss daran wird das Förderband wieder erfolgreich in Betrieb genommen und ein Produktionsmitarbeiter quittiert Herrn Meyer den Einbau digital auf seinem Handheld. Zeiten und verbrauchte Materialen wurden hierbei bereits automatisch in den Auftrag überführt.
Auf einen Blick wird klar: Der neue Prozess ist deutlich effizienter als das konventionelle Vorgehen. Er braucht weniger als halb so viele Schritte. Statt in 12 Schritten lösen Sie Ihr Problem in 4 Schritten. Unterstützen Sie Ihre Instandhaltung mit mobiler Technologie, nutzen ein enormes Einsparpotenzial, das viele Unternehmen immer noch unbeachtet liegen lassen.